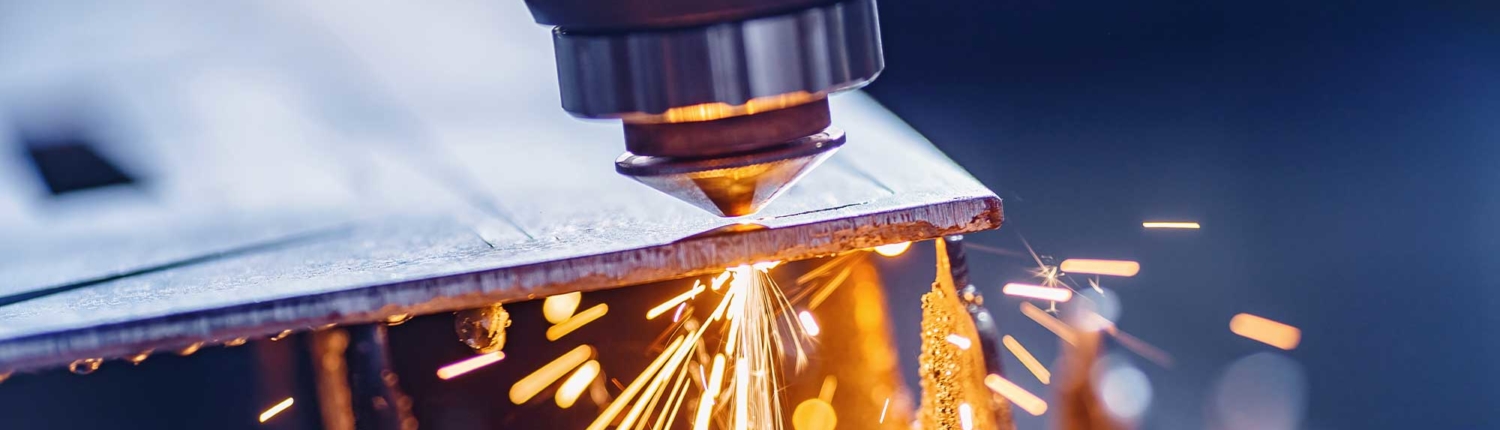
Benefits of Robotic Welding
Welding is a dangerous profession—it exposes skilled workers to extreme temperatures and toxic metal fumes. Using a robotic welding system is a great way to reduce employee injury, ensure quality, and increase output. There are many benefits of using an automated welding process, including:
Increased safety: Welding is a high-risk profession, and employees can suffer from life-threatening injuries. You can’t replace humans, but you can repair robotic welding equipment. Automating the welding process reduces employee injuries and creates a safer work environment.
- Quick completion: Experienced welders can tackle complex projects at a fast pace. However, welding is an exhausting profession; after hours of work and concentration, welders slow down. Using an automated welding system ensures that work is completed in a consistent time frame.
- Consistent weld quality: Robots aren’t prone to human error—they perform welding tasks the same way every time. Using an automated welding system ensures that multiple welding tasks will be completed with the same precision and won’t be affected by distraction, error, or physical exhaustion.
- Lower labor costs: Becoming a welder is not an easy process, and there are many areas of the country that don’t have enough skilled workers for their welding needs. Labor costs can be steep in these areas. Robotic welding systems eliminate the cost of hourly wages and can work at all hours of the day.
Disadvantages of Welding Robots
There’s a reason why fully automated welding systems haven’t entirely replaced skilled welders. Both automatic welding and manual welding have their pros and cons. Some of the benefits of robotic welding can become cons for certain projects, including:
- Lack of flexibility: Robotic welding systems are great for simple, repetitive tasks that are quick and easy to accomplish. For more complex projects, workers need specialized knowledge to determine how to tackle a project. Plus, welders can jump straight into a project, whereas automated systems need adjustments for each job.
- Lost productivity during repairs: If a robotic welder malfunctions, you’ll have to call for a repair or replacement. When a worker is sick, injured, or unavailable, another team member can fill in on any project. Lost productivity during a repair can push your project timeline back and reduce profits.
- Lack of problem-solving: Because welders spend many years mastering their skills, they can spot various issues and react appropriately. Whereas a machine will keep going until it breaks, a skilled welder will stop to evaluate the problem and carefully determine the next steps.
- Cost: Though you don’t have to pay a robotic welder an hourly wage, the up-front cost of renting or buying equipment can be significant. Additionally, complex machinery repairs are expensive, and production ceases during repair, which can end up costing more than you thought you would save in wages.
Deciding if Welding Industrial Robots or Manual Welders Are Best for Your Project
Though robotic welding systems and manual welders can perform some of the same functions, there are scenarios in which one will fit your project better than the other. For metal fabrication processes that are straightforward, welding robots can speed up the process and uphold high weld integrity during every project. Robot welding is also perfect for high-quality spot welding in settings with fast production.
For complex welding projects with many steps, human welders cannot be replaced. If a project requires decision-making, problem-solving, and adaptability, an automated process won’t work—skilled welders must use their critical-thinking skills and years of experience to complete the project successfully. Robot welders are only the right option if they are needed to perform a single task repeatedly, and in many cases, humans can perform this task just as well. Sometimes, the high cost of automated welding systems outweighs the benefits they provide.
Oxygen Service Company Is a Top Provider of Automated Welding Processes
Oxygen Service Company is here to provide manual welding tools, robot welding systems, and high-quality equipment repairs for any project. Our team of certified welding machine repair technicians can tackle any repair and get your project back on track. Oxygen Service Company also employs a skilled team of engineers that can provide guidance on using and optimizing robotic welding systems.
For over 60 years, Oxygen Service Company has provided welding equipment and solutions to the top construction and manufacturing companies. We can help you maximize productivity, reduce costs, and prevent equipment breakdowns to ensure your project goes smoothly. Contact us today to learn more about our equipment, repair services, robotic welding systems, and how we can make the most out of your welding project.
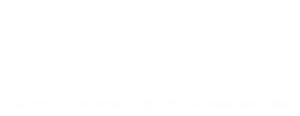