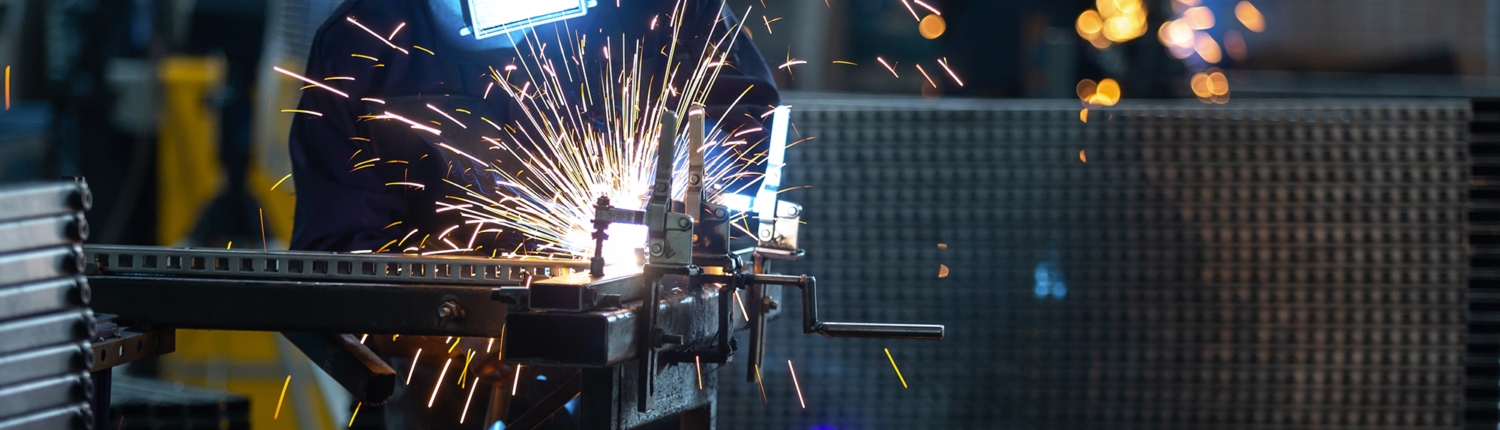
Welding is an essential process in many industries, but it can also be a dangerous one. Understanding and implementing proper welding safety measures is crucial to protect both the welder and those nearby. In this comprehensive guide, we explore the key elements of welding safety and provide best practices to ensure a safe working environment. We cover it all, from understanding the importance of welding safety guidelines to identifying and mitigating the top welding hazards.
Whether you are a beginner welder or an experienced professional, this guide will provide valuable insights and resources to keep welding safety at the heart of your work.
The Importance of Welding Safety Procedures
In harsh occupational environments like welding, safety precautions must be strictly followed. Physical hazards, including electric shock, fire, and exposure to poisonous gasses, are constant, but so are the chances of accidents that can lead to loss of critical production time.
Safety should be a welder’s top priority. Without using personal protective equipment (PPE) or following safety precautions, welders risk their lives and their coworkers’ safety. This is true whether one works for a billion-dollar manufacturer or a small-scale operation.
Understanding how to use equipment and address common welding hazards is a great way to promote safety in the workshop. With enough knowledge and resources, welders can effectively protect themselves and those around them.
The Top Welding Hazards—A Brief Overview
Some of the most common welding hazards include the following:
Electric Shock
Electric shock, one of the most immediate and deadly risks in the welding process, can result from direct contact with electrical parts or improper use of equipment.
Toxic Fumes & Gases
The process may release numerous harmful gases, making proper ventilation and the use of appropriate respirators indispensable.
Fires and Explosions
Welding sparks can easily fly off and ignite flammable materials, causing fires or explosions within a considerable radius. Crucial fire safety tips for maintaining a safe environment are crucial in this occupation. All it takes is slag or spatter coming in contact with a flammable object for an incident to occur.
Eye Injuries
The intense light generated by welding can cause damage to the eyes if appropriate eye protection isn’t worn. Arc eye, otherwise known as flash burn, is the most common eye injury in the welder profession. With treatment, the cornea can repair itself in two days. Without treatment, arc eye can lead to infection and loss of vision.
If you notice the following symptoms after welding, seek medical attention:
- Light sensitivity
- Blurred vision
- Bloodshot eyes
- Mild to severe eye pain following a welding incident
Are you searching for a welding equipment and repair supplier? You have come to the right spot. OSC is a top supplier of welding equipment and repair services.
What to Do in the Event of a Welding Accident
Incidents can occur despite having working training and safety precautions in place. When they do, it is crucial to respond effectively. Here are a few tips:
1. Know the Proper Protocol
Ensure you know the emergency procedures at your worksite. If an accident happens, the priority should be to ensure your safety and the safety of those around you before anything else.
2. Report the Incident
Notify your supervisor immediately. Timely reporting of incidents helps in reducing potential future hazards.
3. Get Help
Finally, seek immediate medical help if necessary. In some cases, symptoms from inhalation hazards or burns may not appear until hours after exposure.
Welding Safety Best Practices to Follow
While understanding the potential hazards is half the work, implementing effective safety measures is equally as important. Start with the following tips:
1. Secure Adequate Personal Protective Equipment (PPE)
The first step is to equip oneself with the necessary PPE. This includes welding helmets, gloves, and proper work gear to protect the worker from physical hazards. Items like welding helmets protect workers from physical hazards and reduce the risk of eye injuries from sparks or severe light exposure. Similarly, high-quality, fire-resistant welding gloves are great for shielding workers’ hands from electrical shocks, extreme heat, and sharp objects.
2. Invest in Sufficient Equipment
Various technological advancements have introduced new safety equipment into the welding industry, which can better protect workers and increase overall safety standards.
3. Conduct Frequent Safety Checks and Maintenance
Regular safety checks and maintenance of equipment ensure that the tools and machines used by computer numerically controlled tool operators are in good working condition and pose minimal risk.
4. Keep Your Environment Clean and Safe
The welding environment itself must be made safe by following fire safety tips such as removing all flammable material from the vicinity and ensuring the availability of firefighting equipment.
5. Conduct a Welding Risk Assessment
Before commencing a welding task, a thorough risk assessment should be performed and the necessary safety measures determined and implemented.
Key Takeaways
- Welding is an essential, yet incredibly hazardous field that should be approached with caution.
- Being able to identify common welding hazards and the protocol to address issues is key to maintaining a safe environment.
- Always prioritize proper equipment use and maintain a safe, clean environment with routine safety checks.
Oxygen Service Company Keeps Welding Safety at Heart
Your options for affordable welding repairs and equipment are limitless, but high quality is not as easy to find. Oxygen Service Company delivers fast, affordable, and superior welding solutions. We help you avoid costly downtime with welder repair services and prevent welding machine failure with reliable welding equipment rental options.
Welding is a process that requires high-level skills and experience. Before you hire a welding professional to take on a project for you, our certified welding inspector services ensure you have chosen a qualified professional by testing their procedure and measuring it against industry standards.
Learn more about our solutions and contact us today.
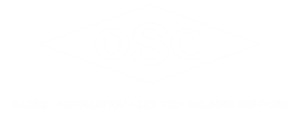