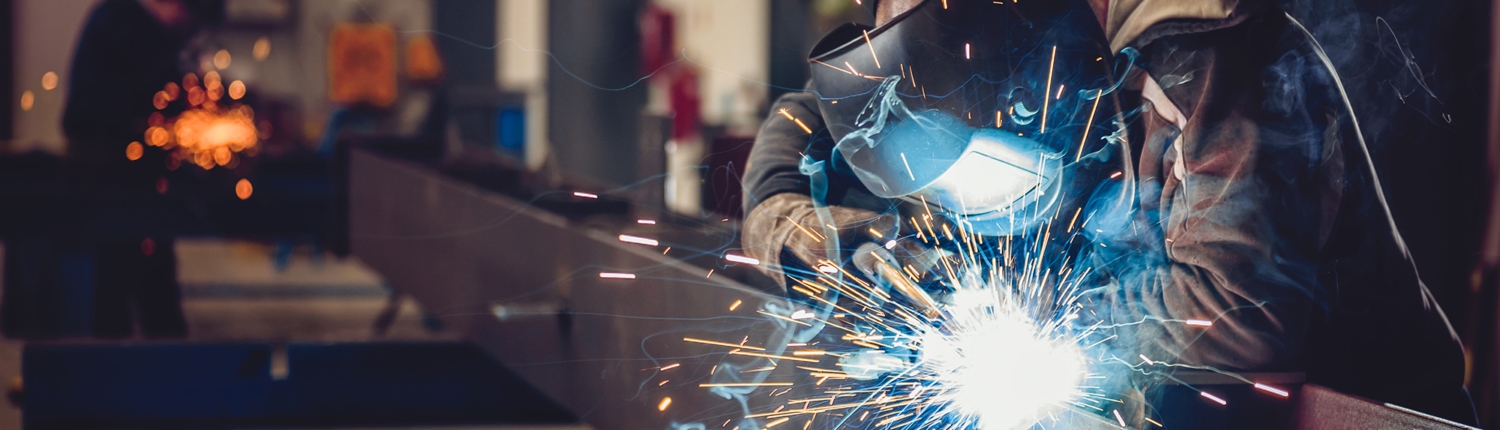
If you want to ensure long-term success for your facility, you need calibrated and certified welding equipment. Calibration measures your equipment’s effectiveness and identifies weak points in your tools. Learn how to use welding machine calibration to improve your welding procedures and provide quality assurance.
Why You Should Know How To Calibrate a Welding Machine
When was the last time you calibrated your welding equipment? If your answer isn’t “before the start of your last welding process,” you’re overdue. The welding industry is demanding, and without adequately maintained equipment, it’s impossible to provide your customers with the high-quality welds they deserve.
Not even the most skilled welder could perform a precise welding procedure with equipment that hasn’t been carefully calibrated according to proper maintenance guidelines. Your welding machine is at its best when it’s treated by certified welding inspectors and has an up-to-date certification. If you want to avoid creating an environment for your workers where frequent machine errors are the status quo, make calibrating your equipment a key part of your welding process.
The Benefits of Calibrating Your Welding Equipment
Calibrating your welding tools helps you keep customers. That should be enough reason for any certified welder (CW) to maintain their equipment. Working with machines in disrepair leads to costly mistakes that need to be fixed with corrections—an extra step that throws off your budget and project timeline and frustrates your clients. Welding equipment in mint condition helps you avoid downtime and increases your skilled welders’ productivity, accuracy, and consistency.
Here are the key benefits of calibrating your welding tools:
- Promotes safety in your facility
- Controls dangerous emissions
- Ensures the accuracy of measurements
- Provides a consistent and high-quality product
- Minimizes drift
Section Two Call To Action. This is prompting the user to either contact the client or driving them to a further in depth page.
Using a Welding Machine Load Bank To Calibrate Your Tools
To calibrate a welding system, you need to connect the equipment to a calibration station. The station measures the wire feed speed, voltage, and amperage of the tools and determines the gas flow rate of the welding source. Once the data has been gathered, the station software compares the values against the operating standards set by the American Welding Society.
A load bank test ensures your welding equipment can operate at a high level and maintain power without shutting down. It also identifies any weaknesses or other issues in the hardware, making it easier to address the problems with routine maintenance. Carrying out the test in a controlled environment and providing proactive treatment helps you avoid long-term costs. You have peace of mind that your welding machine can handle workload stress without malfunctioning.
The Role of Welding Machine Certification in Quality Assurance
There’s more to welding machine maintenance than passing the calibration test once. Certified welders (CW) in the industry must calibrate their equipment routinely. The quality assurance process for welded products is detailed by the ISO 9000 series and the EN ISO 3834-2. Manufacturers who meet the requirements for welding certification are in a better position to grow their reputation and build trust with customers.
Ensuring your equipment is in good condition is a commitment. Supporting your equipment with system maintenance by an accredited test facility may cost you time and money. Still, the reward is high-quality equipment that contributes to your company’s long-term success and productivity. Poorly maintained tools are dangerous and can harm your workers and jeopardize your projects. With a dedication to product quality, you can uphold your reputation and keep your customers’ trust.
Avoid Welding Machine Failure With Oxygen Service Company
Welding machine malfunction isn’t unavoidable. You’ll always get the job done well and right on time when you have quality equipment and a maintenance strategy. Oxygen Service Company specializes in welding equipment rental, repair, and inspection. We support facilities with fast and affordable services that keep your projects on track for success.
Our programs are detailed and extensive, whether you need welding machine calibrations, plasma cutter repair, or preventative maintenance for your welding and cutting equipment. We’re certified welding inspectors at your service. Ready to get your tools in order? Reach out today.
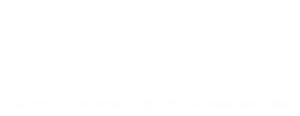