What Are Welding Robots?
The robotic welding market size was $5.42 billion in 2020, and according to Fortune Business Insights, the market is poised to grow from $5.8 billion in 2021 to $9.76 billion in 2028. That works out to a 7.7% compound annual growth rate during the forecast period.
Robotic welding is an automated process leveraging mechanized programmable tools to weld and manage the sector’s equipment. Industries like automotive, oil and gas, and construction are adopting industrial robots. Companies are achieving more sales by rolling out advanced robotic technology and automating processes to manufacture products.
Fortune Business Insights adds that the increasing adoption of robotic welding systems is expected to generate growth across automotive, aerospace, and other sectors. The systems offer advantages that include competitive unit costs, greater productivity, economized labor cost, better workspace utilization, safety, and flexibility.
Are you interested in learning about welding robots or cobot welding? Continue reading for more.
Manual Welding Vs. Robot Welding
You’re likely aware of manual welding—the process in which a welder uses a machine to combine two or more pieces of metal together. Robot welding takes things to another level by utilizing a welding robot arm to carry out the welding process. There are different types of welding robots, namely automatic welding robots and semi-automatic welding robots or cobots.
Automatic Welding Robots: The parts to be welded together are held stationary so that the automatic welding robot can do its work. Once this step is completed, the welded pieces are inspected before being assembled or packaged.
Semi-Automatic Welding Robots: The semi-automatic robot welding process encompasses some human involvement. But that involvement is much less than in the manual welding process. In the semi-automatic robot welding or cobot process, the machine does the actual welding process. But a human operator loads and unloads parts, oversees the process, and performs quality checks.
Advantages of Cobot Welding
Semi-automatic robot welding is less expensive than automatic robot welding. So, cobot solutions could be ideal if your business wants robot welding capabilities but can’t afford automatic robot welding technology.
Automatic robot welding will boost productivity more than semi-automatic robot welding. And since human intervention isn’t needed, you can avoid human errors that jeopardize quality and increase costs.
Let’s take a look at more benefits of cobot welding:
Increased Productivity
Using robot welding technology means greater efficiency and productivity. Reducing—or even eliminating—human interaction means fewer errors compared to what can be expected with a strictly manual welding process. One of the important metrics in melding is arc-on time, which refers to the amount of time welders actually spend on the primary task of welding. The average on-arc time is between 30% and 40%, but that to between 60% and 80% with robot welding. In fact, one robot with a human operator can usually replace two manual welders.
Consistent Quality
Another advantage of cobot systems is that you’ll get a consistent level of quality. One of the reasons the on-arc time for manual welding is lower than that for robot welding is that humans get tired and get distracted. While the aforementioned range is an arc-time of between 30% and 40%, sources say the average is actually closer to 10%. But robots don’t get tired or distracted. They won’t suffer on-arc drops mid-work shift. So, quality won’t suffer.
Cut Down on Waste
When welding is done manually, there will likely be more mistakes that lead to waste. You can’t afford to throw money away due to human error in today’s business environment. But cobot welding systems can drastically cut down on the number of mistakes made. Fewer mistakes mean less waste, and less waste means greater efficiency, productivity, and cost savings.
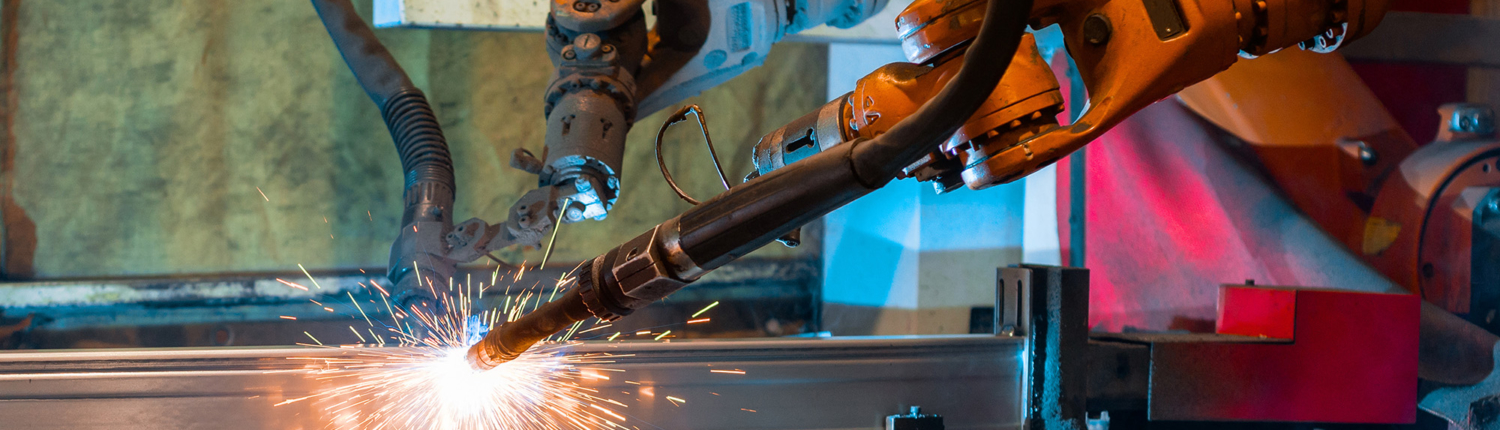
Ways Cobot Welding Can Help Your Business
After looking at what welding robots are and the advantages of using them, it’s important to consider how this technology can help your business. Continue reading to find out more about cobot automation.
Do More With Less
One of the benefits of welding robots is that it’ll help you do more with less. Are you having trouble finding skilled workers for welding positions at your business? Do you sometimes have to turn down orders because you don’t have the manpower to do them? The Great Resignation isn’t over yet. Over the past couple of years, it’s a trend that has seen many employees resign in search of greener pastures. But many employers have been stung by this development. One option is to invest in cobot welding that can help you do more with fewer staff members.
Get the Right Fit For Your Business
Do you need automatic robot welding tech, or do you need semi-automatic robot welding tech—also known as collaborative robots or cobots? You’ll want to explore your options to find the perfect fit for your business, because one size does not fit all in this instance. If you want to get started sooner rather than later and have a tight budget, consider cobot welding.
More Efficiency and Productivity
Getting welding robots is about boosting efficiency in your manufacturing facility or warehouse. You can program them to handle repetitive tasks, and these welding robots will get the jobs finished quicker than human welders without jeopardizing overall quality.
Get in Touch For All Your Cobot Welding Needs
Are you interested in learning more about robotic automation, welding services, or welding supplies? We have you covered, so get in touch to learn more. You can also check out our website if you’re interested in learning more about robotic welding. Whether you already know what you want or have questions and need answers, we’re here to help you. Making a few smart changes or tweaks can help you create a more efficient and productive facility.
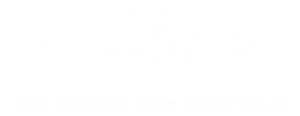