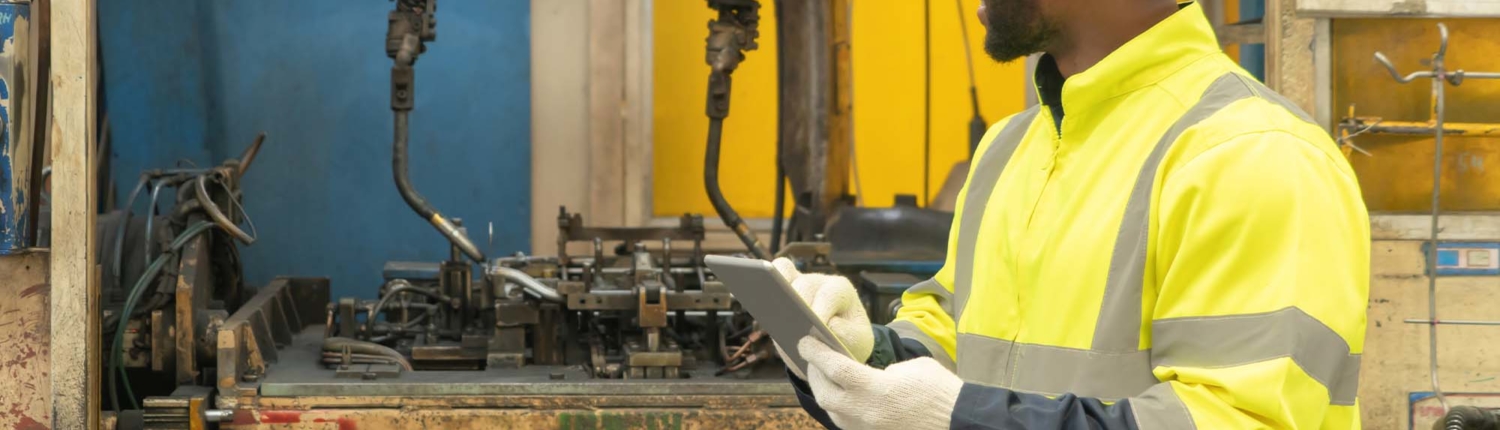
If you’re in the welding industry, you’ve likely encountered weld spatter, but what’s the best way to deal with this common industry problem? Oxygen Service Company has the answers.
Spatter in Welding Explained
Droplets of molten material generated at or near a welding arc are called weld spatter. Known as a nuisance in the industry, spatter is a critical component to avoid when developing an application with the welding process.
Common Causes of Weld Spatter
So what causes weld spatter? Spatter is caused by a number of issues:
- Low-quality material
- Contaminated material
- Welding technique
- Machine settings
- Equipment issues
- Incorrect shielding gas
While several welding inefficiencies cause spatter, the most common cause of it is a disturbance in the molten welding pool during wire transfer. This type of weld spatter occurs when the amperage and voltage levels don’t see eye-to-eye—in other words, if your welding voltage is too low or your amperage is too high for the allotted gas and wire combination, spatter is more likely to develop.
There are also several gases used for welding that increase spatter generation. Using Carbon Dioxide (CO2) for gas metal arc welding (GMAW) is a cost-effective way to increase arc energy, but it creates more weld spatter than other gases.
Problems Caused by Spatter
Weld spatter causes several problems in the manufacturing process:
- Sticks to work pieces or tooling
- Burns operator clothing and skin
- Loses material from the arc and weld
- Increases clean-up
- Higher consumable usage
- Lower MIG wire efficiencies
There are several steps you can take to mitigate spatter generation.
With Oxygen Service Company as your welding provider, you get quality welding equipment and supplies at an affordable price.
Anti-Spatter: A Guide for Weld Spatter Prevention
Use High-Quality Materials
Some welding metals are better than others. Cheaper metal often contains filler to decrease costs, but filler material is often unweldable, making spatter generation inevitable. Do some research and locate high-quality metals that aren’t prone to spatter.
Prevent Dirt and Contamination
If dirt is present during the welding process, the molten metal spatters and leaves you with excessive clean-up. Before you begin a weld, ensure your metal is free from dirt and debris.
You should also consider the type of oil and protective coatings your metal manufacturer uses. While some coatings are welded through seamlessly, others cause excessive spattering. You can remove dirt, oil, and rust from your metals with a grinder, wire brush, or flap wheel.
Cleanliness is needed with your filler material, too. It’s easy to ignore dirt and oil buildup on welding wire or rods stored in your shop, but it’s essential to ensure your filler material is clean before beginning a weld. To prevent filler dirt and contamination, keep your materials in a cool, dry place.
Improve Your Welding Technique
Your welding technique can also increase the amount of spatter generated near the welding arc. If you’re a MIG welder, the angle of your gun can create spatter simply by drifting over a 15-degree angle.
What causes spatter when stick welding? Letting your arc length extend during the stick welding process increases weld spatter.
MIG Welding Techniques
The push/pull MIG welding technique depends on the material being welded. If you need high, consistent heat, pull your weld to prevent spatter. When you need heat distribution, push your weld. Whether you push or pull for a quality MIG weld, your gun shouldn’t exceed a 15-degree angle.
Stick Welding Techniques
During the stick welding process, keep the arc length equal to the metallic core of the electrode you are using for the stick weld.
For MIG and stick welding, accurate speed is crucial. Moving too fast or slow also increases the chances of spatter.
Check Your Machine Settings
Every weld has optimal settings, and your equipment should be adjusted for the specific weld you’re performing. If the heat and penetration aren’t accurate, you risk disrupting the welding pool and increasing spatter.
MIG Welding Machine Settings
For MIG welding, the wire feed must run as accurately as possible. If the wire is running too fast, the solid wire flows into the pool, which causes a disturbance that results in spatter. If the wire is running too slow, you can vaporize the wire before it gets to the weld.
Stick Welding Machine Settings
For stick welding, your speed is linked to the current and voltage settings. If the current and voltage settings are too hot, you naturally move faster and increase spatter. If the current and voltage settings are too cold, your welding movement becomes rough, forcing you to fluctuate between welding and sticking, which causes spatter and an unsightly weld.
For weld spatter prevention for MIG and stick welding, try dialing in your settings. Practice on scrap pieces of metal to ensure accuracy and quality. It may take some experimenting, but dialing in your machine settings improves your weld and reduces the amount of spatter generated.
Fix Equipment Issues
To produce a quality weld and prevent spatter, your equipment must operate as designed. You can ensure your machine is running properly by implementing preventative maintenance for your welding equipment.
How To Clean Weld Spatter
Unfortunately, spatter can still occur despite doing everything right. When spatter happens, you need to clean it to ensure a quality product. You can use popular welding supplies like a grinder, spatter hammer, anti-spatter sprays, gels, and tape.
Providing You With Anti-Spatter Gases, Tools, and Supplies
OSC knows a variety of industry best practices and materials that mitigate the chances of spatter. We can provide you with the highest quality welding gases on the market, and our knowledgeable team can help you choose the best gas that reduces the chances of weld spatter. With our preventative maintenance program for welding equipment, you can rest assured that your machine is always functioning properly and decrease the chance of spatter. You can also find high-quality, affordable welding supplies that help with weld spatter prevention at our welding store. Please reach out to one of our trained welding experts to solve spatter issues or any other welding problems you may have!
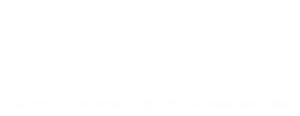